旧ブログで不定期で執筆していたVoice From The Water。
ルアー作りへの想いとかその他諸々、思いのまま書き綴っていたコラムなのですが、新ブログでも始めたいと思います。
今回の新ブログでの一発目のVoice From The Waterは「ルアー素材の声を聞く」という話。
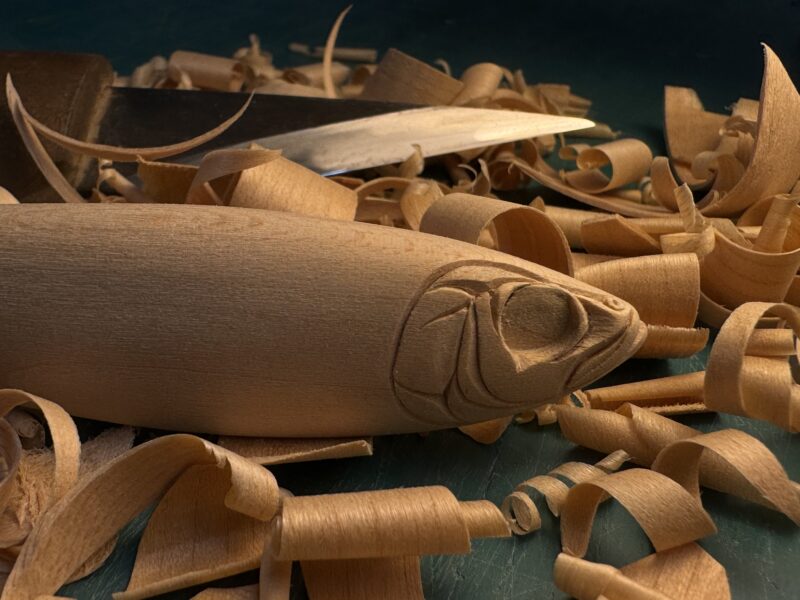
僕自身、中学生の時にハンドメイドルアーを作り始めて40年以上、思い起こせば今まで歩んできた道のりは常にルアー作りを中心にして思考し、歩んできた人生でした。
そして、今も中学生の時と変わらず、大好きなルアー作りを続けられている事にただただ感謝しかないです。(皆様本当にありがとうございます)
そんな僕のルアー製作どっぷり人生ですが、実に様々な素材でルアーを作ってきました。
バルサ製ルアー

この写真のルアー達は中学〜高校生時代に作っていたハンドメイドルアー達。
この頃はバルサ素材を削り出してルアーを作っていました。
当時、ハンドメイドルアー=バルサ材というのが一般的でしたし、ラパラやバグリーズなどバルサ製のルアーが大好きだった事もあり、僕もバルサ材でルアー製作人生をスタートさせました。
もうね、模型屋さんに行ってはバルサの板を一枚一枚確認し、ドキドキワクワクしながら購入していたのを思い出します。
ちなみに写真に写っているルアーですが、写真左上の背中に銀ラメがふってあるルアーはおそらくセミルアーか何かを作ろうとしたんだと思いますが、羽根がカットしてあるところを見るとうまくいかなかったんでしょうw
たぶんですが、この銀ラメもアルミ箔を自分でハサミで裁断して作ってるっぽいですね。
右上のポッパーに至っては何をモチーフにした色なのか、ペンギンかシャチかみたいな不思議な色をしていますw
バルサ材から生み出される強い浮力はルアーアクションを突き詰めていく時にすごい武器になるもので、今も変わらず超重要ルアー素材として使われ続けていますね。
本当に偉大な素材だと思います!
ハードウッド製ルアー

このルアーはエンドウアートクラフトに弟子入りさせていただき、遠藤龍美さんの元で修行させていただいていた時に作ったルアー達。
高校時代からの落差がすごいですねw
遠藤師匠は本当に偉大な方で、リアル系ルアーは今では一般的かもしれませんが、エラなどの造形が立体彫刻されたルアーの元祖は遠藤師匠だと思っています。
一体一体彫刻が施されている上に、ウロコの線も一本一本手作業で刻み込まれているというとんでもない手のかかりよう。。
遠藤師匠がご自身のブランドであるWood Baitを作り上げられたのは1980年代半ばだったかと記憶しているのですが、鳥取の片田舎で雑誌で初めてそのルアーを目にした時の衝撃は今でも鮮明に思い出すことができます。

このブランク達は僕が修行時代にウッドベイトの各モデルを削り出す時に見本にしていたブランク達。
この頃はアガチス、桐、スプールスなどのウッドを削ってルアーを作っていました。

このルアー達は遠藤師匠から独立を許され、自身のブランドを琵琶湖のほとりで立ち上げて製作したドリームラッシュ達。
手前のアユカラーのペンシルベイトが滋賀の工房で作っていたモデルで、後ろのブラウントラウトカラーがカナダで作ったモデル。
滋賀製のドリームラッシュは、ジェルトンというかなり浮力があって切削加工もやりやすい木材で製作していました。
カナダに渡ってからはジェルトンがカナダで入手困難ということもあり、バスウッドという木材に変更。
バスウッドはバードカービングをされる方もよく使われている木材で、ジェルトンでは彫刻が難しい鱗などの細かい細工にも耐えてくれる素晴らしい素材。そんな彫刻に適した素材特性が僕自身の彫刻技術も育ててくれました。

このルアーはシマノさんとお仕事をさせて頂いていた時に作ったトリプルインパクトの原型になったウッド製プロトタイプ。
立体ウロコを彫刻できるようになったのはバスウッドとの出会いが大きかったです。
カナダではこの他にも、レッドシダー、イエローシダー、アスペンなど色んな木材を試し、それぞれの木材の特性を学んでいきました。
ちなみにここまでの時点で、僕が手削りで削ったウッドルアーの総数は修行時代とドリームラッシュ時代を合わせると2万本ぐらいに達していたと思います。
2万体のルアーをナイフで削り出し、一体一体にエラ彫刻を施し、ペーパーをあて、アルミなどを貼り(時には銀箔や金箔なども)、貼った箔に1本1本のウロコ線をナイフで刻み込んだり、あるいはピンで引いたり、僕はルアー作りの才能はあるとは思っていませんが、それらの地味な作業を飽きることなく続けられる耐久力の才能だけはあったかな、と思っています。
そんな僕が向き合ってきた様々な木材の中で最もルアーに適していると思った素材ですが、それは日本の桐材だと思っています。

軽くて水も吸いづらいという特性から、桐材といえば桐ダンスが有名ですが、ルアー素材としても抜群の相性で、軽さといい、耐久性といい、本当に素晴らしいの一言です。
ですが、ルアーを作る時に最強に仕上げづらい木材の筆頭も桐材。
桐材は硬いところと柔らかいところが木目となって積層していて、ナイフの刃の走りは安定しないわ、サンディングしたら柔らかいところばかり削れてデコボコになるわで、綺麗に仕上げるのが本当に難しい素材です。銀箔貼り仕上げなどと同じく、製作者の技量が問われる素材ですね。
ハードウッドはそれぞれの木材で特徴が微妙に異なりますが、水に絡みつくようなアクションを出しやすいのが特徴で、素材がしっかりしていて彫刻に耐えられること、強度が出しやすいことなどが利点だと思います。
鉛製ルアー

このルアーは鉛で作ったジグ。
カナダに渡った当初、本当に生活に困窮し、このルアーを作って魚を釣って自給自足で生活していた時期がありますw
まさに生命維持の必要に迫られて作ったルアー達です。
そんな切羽詰まった状況でしたから、このルアーには何かが宿ったのか、実によく釣れて無事に生き延びることができましたw
そんなジグ作りですが、それまで鉛とか扱った事がなかったので、シリコンモールドの作り方や鉛の流し方などをこのジグ作りで学びました。
当時はYoutubeとか無かったので、電話帳でシリコンラバーを売っているお店を探して実際に行き、お店の人にどのシリコンラバーが向いているかとか教えてもらうのが精一杯の方法だったのですが、当時お金も無かったけど、それ以上に無かった英語力でよく成し遂げられたもんだと、今になって思いますw
鉛は金属でありながら容易に形状を作り上げられるのが最高に良いですね。
ちなみに僕自身は、鉛以外にもルアー素材として非常に可能性を感じている金属があるのですが、それは2025年にお披露目させて頂けるかと思います。
発泡ウレタン製ルアー

ニシネルアーワークスを立ち上げて製造を始めた発泡ウレタンルアー達。
発泡ウレタンでルアーを作るのももちろん初めてでしたが、シリコンモールド作りはジグ製造の時に身につけていましたから、その経験が随分と役に立ちました。
しかし発泡ウレタン素材の研究は挫折の連続で、入手できる限りの材料や思いつく限りの製法を片っ端から試しては失敗しての繰り返し。
そんな試行錯誤を繰り返しながら素材の特性を学び、自分が作りたいルアーにあった調合法や製造法を編み出していきました。
この発泡ウレタン、とりあえずA液とB液を混ぜたら発泡が始まって固まるのですが、実際にやってみると、気温や湿度や混ぜ方の違いで固まり方が変わりますし、発泡ウレタン素材の製造ロットによっても発泡具合が違ったりします。まぁ、プラスチックではありますがナマモノみたいな感じですね。
ちなみにNLWで使っている発泡ウレタンですが、固まったら無臭になりますが、混ぜる前の液体の時はカッパえびせんみたいな匂いがするんですよ〜(どうでもいい情報w)

NLWを立ち上げてあと少しで19年、一体何個のルアーを作ってきたのか‥‥
この発泡ウレタンルアーも僕の地味作業耐久能力という才能をいかんなく発揮して製造を続けていますw
ちなみにそんな発泡ウレタンですが、実はバルサ材と同レベルか、もっと軽量化も可能で、超強力な浮力を稼げる可能性を持った素材だというのはあまり知られていないことかもしれません。

このルアーはそんな発泡ウレタン素材が持つポテンシャルを最大限に開放して作り上げたファットブル8というルアー。

完成品が見つからないので仕上げ前の写真しかありませんが、ファットブル4もその特徴を最大解放して作り上げたモデル。
実際にこの二つのモデルを投げられた事のある方はご存知かと思いますが、この二つのモデルはバルサクランクと比較しても全く引けを取らないアクションレスポンスを実現できているかと思います。
具体的にこのモデルに何を施したかというと、フレームなどの補強体を入れない事で限界まで浮力を稼ぎ、その稼いだ浮力に対してカウンター的に重たいウェイトを入れ、アクションレスポンスの向上を図っています。
そんなことが可能なのであれば、他のモデルにも取り入れればいいじゃんという感じではありますが、実はそれができない理由がありまして、発泡ウレタンは比重を軽くすればするほど強度が落ちるのでフレームなどの補強体を入れないとボディー折れなどの破損につながってしまうんです。
ですが、ファットブルはボディーが太いので補強体を入れずとも強度が出せて、浮力を最大限活かせる構造体を実現できたという事であります。
そう考えると、バルサって本当に凄い素材です。
比重だけで言えば、発泡ウレタンでもバルサと同等かそれ以上の浮力を出せますが強度が追いついてこないんですよね。
バルサの凄いところはスカスカで圧倒的に軽い素材なのに折れにくい事。
その秘密は自然素材の木材が持つ繊維の力だと思っています。
なので、例えばですが、渓流用の小さめで細身のミノーなど、強い浮力と強度の両方が要求されるようなルアーにおいては、僕自身はバルサを超える素材は今のところ無いかなと思っています。
話を発泡ウレタンに戻しますと、この素材の利点は、浮力をバルサのようにもハードウッドのようにもできる比重調整の幅の広さを持つことと、モールドを使って成形する事で、細かい外観仕上げを実現できることだと思います。
発泡具合の調整など取り扱いが難しいところもありますが、天然素材よりはバラツキを抑えられるというのも良い点ですね。
ソリッドプラスチックルアー

この写真のルアーはSCスメルトというルアー。
このルアーは内部に気室を持たず、発泡ウレタンのような素材浮力も持たないソリッドプラスチックで作り上げたモデルです。
ソリッドなのでもちろん浮力はゼロ。
浮力に頼れないという意味では、鉛のルアーと同じですね。
ボディーシェイプ、ウェイトバランス、タイングアイの設定など、浮力に頼らないバランス出しはとても奥深く、僕的にはチャレンジ精神を大いに掻き立てられるカテゴリーでもあります。
このソリッドルアーで学んだ技術を存分に取り入れたルアーを世に送り出す準備が整ってきているので、楽しみにしていてください。
中空ABSルアー

現在のNLW製品の主力でもある中空ABSルアー達。
僕が初めて中空ABSルアーに携わらせて頂いたのはシマノ社とお仕事させて頂いた2000年初頭に遡りますが、中空ABSルアーに関して書き出すと、とてもここでは収まらないので、それはまた今度機会を設けて書いていきたいと思います。
一つだけ簡潔に言えることがあるとしたら、同じハードルアーという形をしていても、ウッドルアーや発泡ウレタンルアーなどの浮力体で構築されたソリッドボディーと、気室を確保して浮力を生み出している中空ABSボディーでは開発のプロセスもバランスの出し方もだいぶ異なるということですね。
その辺も今度掘り下げて書いて行ってみたいと思っています。
ソフトプラスチックルアー

現在、NLWではソフトベイトを2機種ラインナップしていますが、ソフトベイトの世界も本当に奥が深いです。
ハードルアーとの決定的な違いは、当たり前すぎてこうやって書くのも小っ恥ずかしいですが、ソフトベイトは形状が変化するところw
ハードルアーにおいてのボディーシェイプって、そのボディーの特性やポテンシャルを決める超重要な要素なわけですが、ソフトベイトの場合はそのボディーシェイプが水流を受けて変化しちゃうわけです。
しかも、使用する素材の柔らかさの違いとかがアクションにダイレクトに影響を与えますし、塩など何かを練り込むと素材の特性そのものが大きく変わってきたります。
そもそも素材自体が塩化ビニール系の樹脂とか、エラストマーとか、製法もインジェクションだったり、ハンドポアだったり、その奥深さはハードベイトに負けていないと思います。
中空ソフトプラスチックルアー
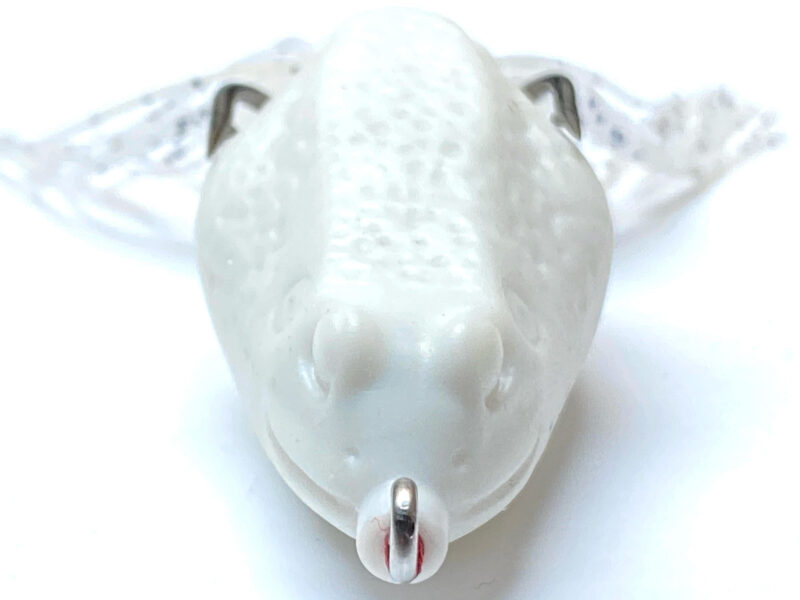
まだリリースまで漕ぎ着けられていませんが、中空のカエルさんもここ4年ぐらい研究を重ねています。
中空のソフトボディーをどうやって作ったらいいの?というところから研究を始めたフロッグ開発ですが、試行錯誤を繰り返しながら、中空ソフトボディーならではのメリットやデメリットなどを学んで行っています。
そして、現在の状況は、中空フロッグを作る上でどうしても克服したかった構造上の弱点を理想的と思える形で克服できる方法がようやく見つかり、そのシステムを量産の場で再現するべく工場で研究して頂いている段階まで漕ぎ着けています。
色々と機密事項なこともあって、今はこれぐらいしかお話しできなくて申し訳ないですが、その時が来たらお話しさせて頂きますね。
まとめ
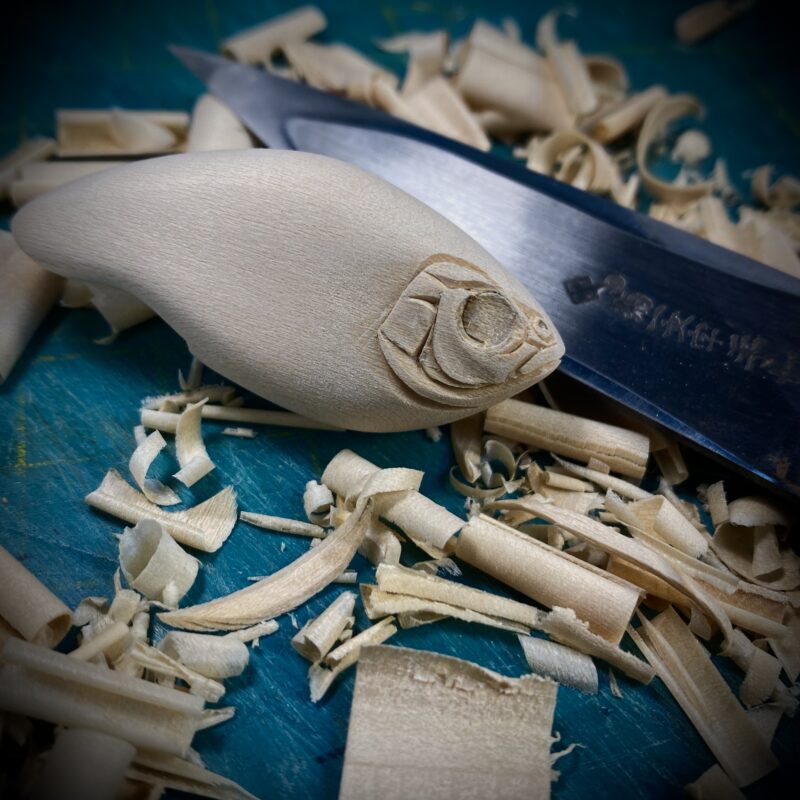
様々な素材と向き合いながらルアーを作ってきた僕ですが、僕の場合、木を削り出すところから全てのルアーの開発が始まります。
まずは木を削って形を彫り出し、そこを出発点にして作りたいルアーに合わせた開発方法やプロセスをとっていくというやり方ですね。
前述した通り、木を削って削って削りまくってきたわけですが、そういう日々を積み重ねてきた結果、ルアーを削るという動作は自分の中では呼吸をするのと同じぐらいの感覚に近く、感じるままに自然の流れに身を任せて無心で淡々と彫り出すという感じです。
そこにはドラマの演出のような魂のぶつかり合いみたいな光景はありません。
埃まみれのおっさんがただ淡々と削っているだけですw
うまく言えませんが、ナイフの最初の一太刀を木材に入れた時に、その木材がルアーになりたがっているのを感じられるかどうか、ホントうまく言葉にできませんが、木材の中で眠っているルアーからの声を聞く(感じる)とでも言ったらいいのでしょうか、その感覚をとても大切にしてルアー作りと向き合っています。
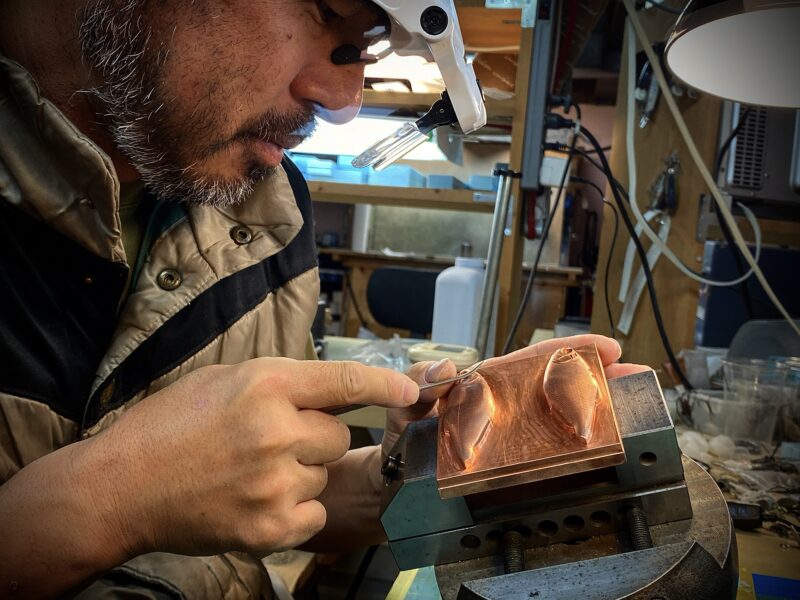
この写真は量産用の金型を作る時の放電加工に使う銅電極を手作業で仕上げている作業風景。(ルアーはシムコー75)
削るのは木だけではなくプラスチックの塊も削りますし、銅の塊の彫刻なども行なっています。
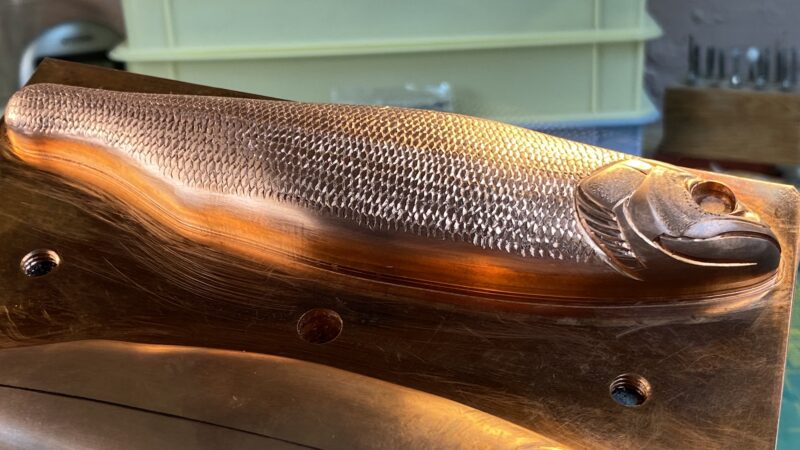
この写真のモデルはダイワUSAさんとのコラボで作らせて頂いたマスキー用のBessieというルアーの銅電極に手作業でウロコを一枚一枚彫り込んだもの。
僕の日常はこんな感じです。
まとめのまとめ
最後のまとめとして一つだけ僕に書ける事があるとしたら、素材にはそれぞれの持ち味があり、それを活かすも殺すも作り手次第ということでしょうか。
例えば、クランクベイトで言えばバルサクランクと中空ABS製クランクのどっちが優れている?みたいな話では全くなくて、素晴らしい完成度の名作バルサクランクもあればイマイチなのもいっぱいあるし、それは中空ABS製クランクでも同じです。
要は適材適所ということだと思っています。
目の前に並んでいる素材達が発している声に耳を傾け、何かを感じ取り、作り手としてそれをどう活かしていったらいいのか‥‥
どこまで行っても未熟、どんなに努力を重ねてもゴールには決して到達できない戦いではありますが、それは同時に最高にワクワクする戦いでもあります。
そんな気持ちを忘れない限り、きっと昨日よりは今日、今日よりは明日とちょっとずつでも成長していけるんじゃないかなと思いながら、今日もルアーを作り続けています。